The recent upgrade is a key part of ground handling service provider Alyzia’s goal to serve more flights and optimize baggage handling while guaranteeing safety. Partners in the deployment are Alvest Group, TLD and Smart Airport Systems for the vehicle, EasyMile for the driverless technology and Alyzia. The goal is to demonstrate how autonomous vehicles can optimize luggage and freight logistics. By removing any human intervention on board, cost and time efficiency, scalability and flexibility are all unlocked.
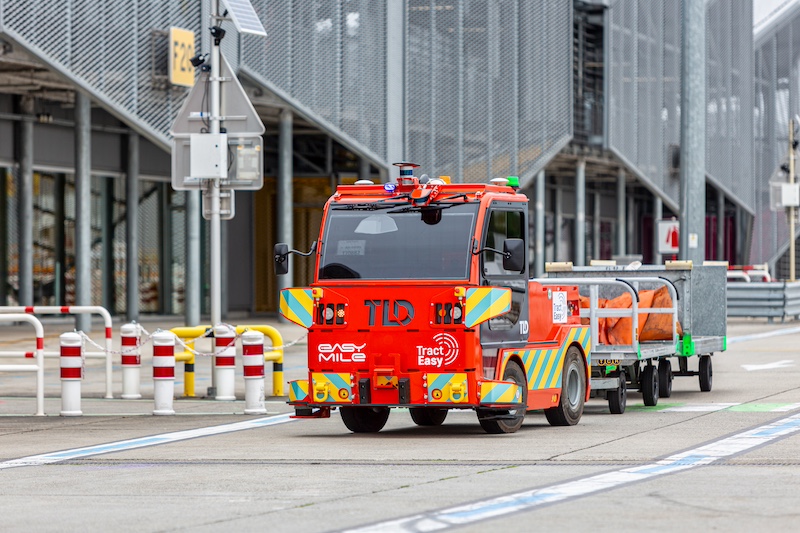
The original brief/ODD and what changed
Toulouse-Blagnac wanted to find a solution that proved they could optimize their flow between the baggage gallery and the aircraft parking positions.
Now, following the move to L4 operation, the worker who was previously the onboard attendant can instead monitor missions from a tablet. Other workers can use a rear panel on the vehicle to send it anywhere on the programmed line. On this line, each station is named like an aircraft gate so they are easily recognizable to workers.
This is part of the beauty of autonomous solutions – they are easily adaptable and integrable to existing systems and layouts, and can run with human-driven vehicles, etc. It also means that other vehicles could easily be added for fleet expansion or peak times.
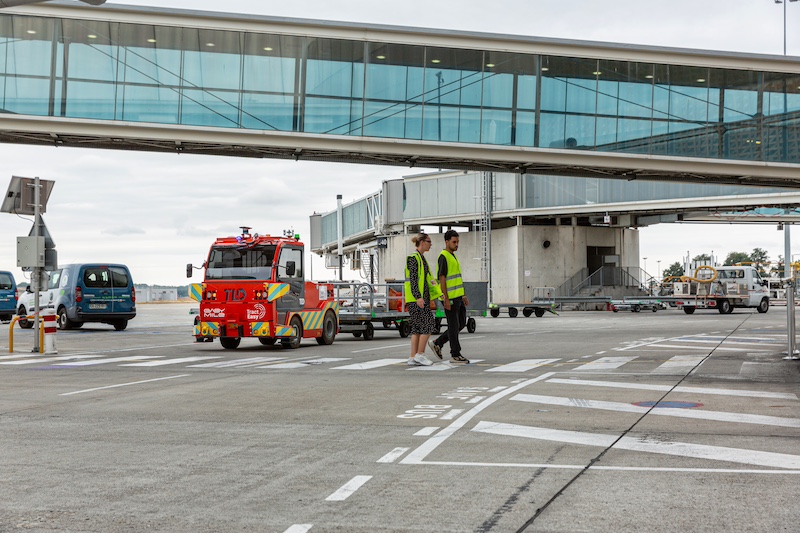
New tasks and challenges
The key task is to unload baggage from aircraft. The challenge comes in the luggage gallery, as it is narrow and crowded so the vehicle needs to maneuver very carefully.
Another challenge is running around aircraft and behind them as they are parking. The ADS-B system needs to work well and special insurance policies have been taken out for these positions.
What about safety?
This service is only monitored from a tablet. However, remote operation is a possibility depending on the use case. In the event of a potential hazard, it will always take the safest measure, which can include stopping. In this case it usually restarts automatically. There are also alerts on the tablet to indicate any issue. There have been no accidents to date.
What’s on board of the EZTow autonomous tow tractor
The vehicle body itself is manufactured by TLD, a leading manufacturer of baggage tractors for airports, with nine factories around the world and over 1,800 employees. It is a robust and known platform that can tow up to 25 metric tons and has a 4.25m turning radius. The vehicle is fully electric with lead acid or Li Ion batteries. EasyMile has taken a conservative approach to the sensor suite, using devices from a number of market leading suppliers, but is not committed to any particular technology or supplier and regularly implements updates. We use what we think gives us the best information on every part of our environment, both close to the vehicle and at longer ranges. Complementing the lidars, the stereo cameras provide input to EasyMile’s deep learning effort, and a separate team adds another redundancy layer in terms of software development. EasyMile’s own programmers write the algorithms that interpret sensor data and apply deep learning techniques to them.
The high level decision making and path planning software runs on a dedicated computer, while the dedicated safety software runs separately to ensure high confidence in the vehicle’s safe operations. Using all the available data from the different sensors in a fusion algorithm, the vehicle knows its position and the accuracy of it to within 23cm at all times. Any potential deviation will safely slow down or stop the vehicle. In addition, the vehicle is in constant communication with both its environment and the EasyMile supervision tablet. EasyMile’s satellite navigation technology is a multiGNSS system that processes GLONASS as well as the original GPS. The system’s precision is enhanced by real time kinematic (RTK) processing. The GNSS position is also used in conjunction with information from the 3G or 4G grid, with 5G testing underway.
The key goals of the project
The goal is to demonstrate the readiness of driverless solutions for commercial operations at airports, phasing them in with the range of manually driven vehicles still in operation. In Toulouse-Blagnac’s case, this means specifically the towing of luggage from landing positions to the baggage hall. The service is also an opportunity to test the EZTow on various airport infrastructure elements such as intersections, roundabouts and turning circles, and in different weather conditions like rain, fog, and snow.
This article was originally posted on: ADAS & Autonomous Vehicle International.